Lorsqu’il s’agit de stocker de la marchandise de petites pièces ou légère, deux types de problèmes se posent :
- Un grand nombre de références, et donc une grande quantité d’unités à trier.
- Un taux de rotation élevé.
Cet article vise à définir les paramètres à prendre en compte pour concevoir le système de stockage le plus adapté aux articles de petites dimensions. La solution la plus efficace et rationnelle est de choisir un système de stockage automatisé. Il ne faut toutefois jamais oublier, lors de la conception d’un entrepôt, surtout s’il est robotisé, de respecter un critère essentiel : le coût de l’installation doit être proportionnel au coût total des opérations. Il est donc nécessaire de trouver le juste équilibre entre le coût et l’utilité.
Afin d’atteindre ces objectifs, chacune des installations possibles doit être rigoureusement analysées.
Les principes clés pour l'installation d'un système de stockage de petites pièces
Lors de la conception d’une installation pour le stockage de marchandises de petites dimensions, deux types de stratégies différentes sont possibles, et peuvent même être combinées : le principe de « l’homme vers le produit » (où l’opérateur se déplace) et du « produit vers l’homme » (la marchandise se déplace).
Il n’existe pas une solution idéale entre ces deux stratégies. Il est même possible qu’il n’y ait pas de solution optimale et que la meilleure soit la combinaison de ces deux principes. Nombre de doutes planent sur cette question à laquelle il est difficile de répondre, car chaque produit, chaque secteur, chaque client à ses propres besoins nécessitant une solution adaptée.
Cet article introduit les principes de bases et présente les différentes options possibles. Cependant, l’avis et la collaboration avec des professionnels spécialisés dans le domaine est indispensable. Chaque cas est unique et ne peut être généralisé sans une étude détaillée du projet.
1. Le principe de l'homme vers le produit
De tous les systèmes existants, le principe de l’homme vers le produit est le plus courant. Avec cette configuration, les produits sont stockés dans des rayonnages disposés en fonction du système choisi. La manutention de la marchandise peut être manuelle – le produit est rangé unité par unité – ou mécanisée, les opérateurs manipulent des unités de charges complètes, telles que des bacs ou des caisses-palettes par exemple.
- Le principal inconvénient de cette stratégie est le coût élevé qu’elle requiert pour le traitement et l’organisation de la préparation de commandes.
- Cependant, son principal avantage, et non des moindres, elle nécessite qu’un faible investissement.
Le picking est généralement réalisé par un opérateur, qui se déplace à pied ou sur un chariot, jusqu’à l’emplacement des références devant être prélevées, conformément aux bons de commande reçus.
Les solutions de stockage privilégiées pour ce principe sont les rayonnages à un ou plusieurs étages (souvent combinés avec des passerelles ou des mezzanines), les rayonnages sur bases mobiles, les rayonnages à allée étroite ou encore des rayonnages dynamiques pour picking.
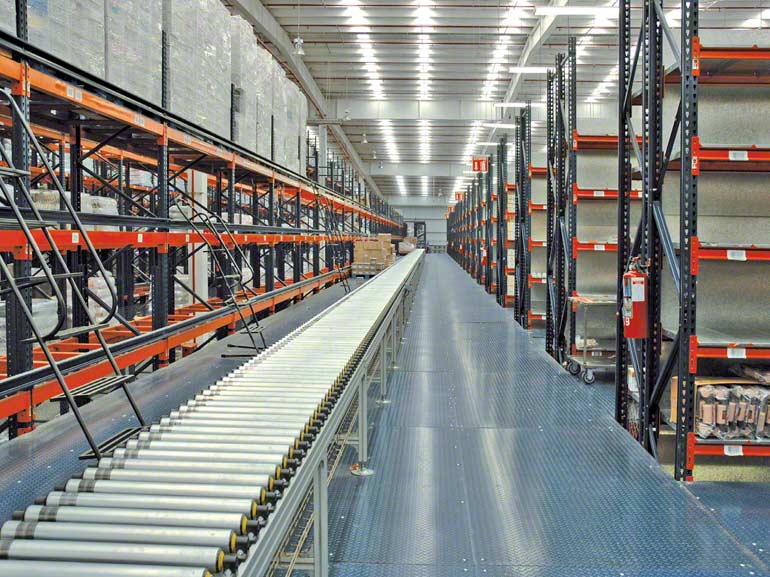
Rayonnages pour picking desservis par un convoyeur à rouleaux
Le degré d’automatisation pour ce type d’installation est généralement très faible et dépend des caractéristiques de chaque système. Seuls les rayonnages dynamiques pour picking équipés de dispositifs « pick-to-light » et les chariots « put-to-light » permettent d’automatiser la préparation de commandes.
Tous les systèmes reposant sur le principe de « l’homme vers le produit » ne sont pas identiques. Les diverses options peuvent être classées selon une échelle allant de 0 à 10, appliquée à quatre paramètres qui sont :
a) Le coût total de l’investissement.
b) Le coût de manutention, à savoir de la main d’œuvre nécessaire à la gestion de chaque unité (qui est indépendant du coût de l’investissement).
c) La capacité de traitement, c’est-à-dire le nombre de cycle par heure.
d) Le taux d’occupation de la zone, en termes de capacité de stockage effective.
Analysons maintenant un par un les systèmes utlisant la stratégie de « l’homme vers le produit », en fonction de quatre paramètres.
-
Les rayonnages installés sur un seul niveau
Les rayonnages installés sur un seul et même niveau ont une faible capacité de stockage, et sont généralement conçus en laissant une allée étroite entre chaque rayonnage pour permettre le passage de l’opérateur et du chariot de picking. Aujourd’hui, il existe des systèmes très sophistiqués qui permettent de placer des bacs aux dimensions et caractéristiques variées et surtout, adaptés à tous les volumes de contenants et aux besoins de chaque secteur d’activité.
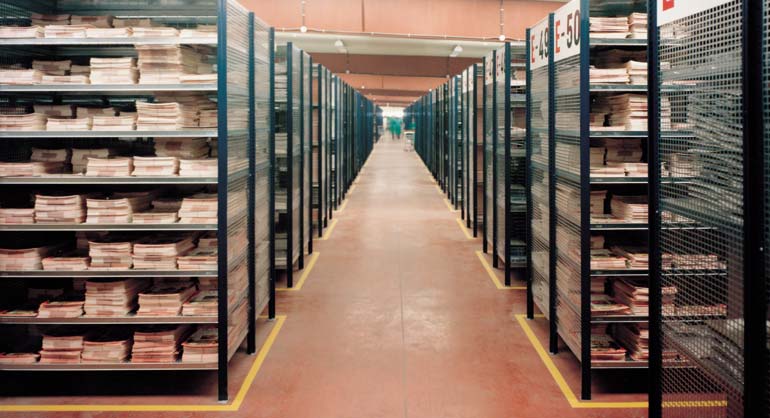
Rayonnages pour le stockage d'archives
Généralement, ces rayonnages ne sont pas très hauts, tout dépend des besoins de chaque secteur et de l’entrepôt, et les niveaux inférieurs sont principalement destinés au stockage des charges les plus lourdes. L’inconvénient des structures très hautes est qu’elles gênent et retardent l’accès aux produits situés aux niveaux les plus élevés. Une bonne alternative, qui peut s’avérer indispensable, est l’utilisation de chariots préparateur de commandes avec escabeau ou d’un escabeau de sécurité roulant. Cependant, la manutention étant manuelle, le picking et le réapprovisionnement des rayonnages en unités est alors lent.
Dans les entrepôts équipés avec ce type de rayonnages, des engins de manutention peuvent être utilisés, tels que des transpalettes manuels ou motorisés, ainsi que des chariots préparateur de commandes à faible ou moyenne élévation.
Evaluation de ce système :
Paramètres | Evaluation | Remarques |
Coût total de l'investissement |
1 |
Fabile |
Coût de la manutention | 8 | Elevée, elle est généralement manuelle |
Capacité de traitement | 4 | Moyenne |
Exploitation de la surface | 3 | Moyenne, compte tenu de la faible largeur des allées. L'exploitation n'est pas optimale |
-
Les rayonnages installés sur plusieurs niveaux
Ce système de stockage repose sur le même principe que le précédent, puisqu’il s’agit de rayonnages superposés les uns au-dessus des autres, installés sur deux ou plusieurs niveaux. Ainsi, comme la hauteur des rayonnages est doublée voire triplée, selon le nombre de niveau, la capacité de stockage est alors bien plus importante.
Ce système supprime l’utilisation d’escabeau de sécurité roulant et de chariots préparateur de commandes avec escabeau, et par conséquent réduit considérablement le temps consacré aux opérations de picking.
Dans les entrepôts dotés de ce système, l’utilisation de dispositifs mécaniques est impossible sauf au rez-de-chaussée ou sur des mezzanines hautement résistantes (cependant, leur coût est élevé). A contrario, les chariots élévateurs ou autres engins de manutention similaires, tels que des élévateurs ou des monte-charges, sont compatibles, notamment pour approvisionner en marchandises les niveaux supérieurs.
- Evaluation de ce système :
Paramètres | Evaluation | Remarques |
Coût total de l'investissement | 1,5 | Faible, mais sensiblement plus élevé que les installations à un seul niveau |
Coût de la manutention | 9 | Elevé, et plus important que pour les installations à un seul niveau. Il est impossible d'utiliser des engins de manutention motorisés pour l'approvisionnement en marchandises et le picking au niveau des étages supérieurs |
Capacité de traitement | 3 | Moyenne, mais inférieur à celle des installations à un seul niveau car la performance des étages supérieurs est réduite par l'absence d'engin |
Exploitation de la surface | 5 | Moyen, en surface il est similaire aux installations à un seul niveau mais son volume est doublé voir triplé |
-
Les rayonnages sur bases mobiles
Les rayonnages sur bases mobiles permettent de gagner de l’espace, car, généralement, seule une allée est nécessaire. Toutefois, si l’accès à tous les rayonnages est fréquent ou si ces derniers sont nombreux, il est possible de concevoir des systèmes comportant plus d’une allée, en regroupant les rayonnages en plusieurs blocs.
L’approvisionnement et le picking des produits s’effectuent exclusivement à la main, et, comme les distances à parcourir sont plus courtes que dans les installations à rayonnages conventionnels, le temps nécessaire pour l’ouverture de l’allée (ou des allées) est largement compensé.
Les rayonnages étant hermétiquement scellés en blocs, la marchandise stockée est protégée de la poussière. De plus, comme son ouverture est automatique, l’installation est équipée d’un système de sécurité qui stoppe automatiquement la manœuvre en cas d’obstacle et ce afin d’éviter tout risque d’accident, notamment le risque d’écrasement d’un opérateur entre deux rayonnages.
Les rayonnages sur bases mobiles peuvent être commandés par un ordinateur : l’ouverture et la fermeture des allées peut être programmées, accélérant ainsi considérablement les opérations.
- Evaluation de ce système :
Paramètres | Evaluation | Remaruqes |
Coût total de l'investissement | 3,5 | Moyen, mais plus l’installation est petite, plus l’investissement est coûteux (par rapport à sa capacité). Ce système peut être installés sur plusieurs niveaux |
Coût de la manutention | 8 | Elevé, l’ouverture et la fermeture facile de l’allée dans les installations automatiques réduisent le temps consacré à la manutention, augmentant la productivité et diminuant le coût de la main d’œuvre par article |
Capacité de traitement | 4 | Moyenne, la réduction du temps consacré aux déplacements augmente le nombre d’articles traités par unité de temps |
Exploitation de la surface | 7 | Elevé, le nombre réduit d’allées nécessaires augmente considérablement le taux d’occupation au sol. Il est même possible de le multiplier avec l’installation d’un système à plusieurs niveaux, bien que cela implique un investissement bien plus important sans répercussion favorable sur le coût et la capacité de traitement |
-
Les rayonnages à allées étroites
Parmi les systèmes répondant au principe « de l’homme vers le produit », les rayonnages avec allées étroites sont ceux qui offrent les meilleurs taux en termes d’occupation au sol, de capacité et de coût de manutention. En revanche, l’investissement pour ce type de solution est plus élevé que les précédentes, bien qu’il reste à des niveaux acceptables.
La surface occupée est très restreinte grâce à la faible largeur des allées entre les rayonnages, qui peut être réduite à 1 000 mm en fonction des types de charge. Néanmoins, il est plus courant d’aménager des allées de 1500 mm à 1 700 mm de large afin de pouvoir gérer des charges complètes. Ces systèmes permettent également de tirer parti de toute la hauteur disponible de l’entrepôt.
Les engins de manutention utilisés sont exclusivement motorisés : chariots à mât rétractable, tridirectionnels, préparateurs de commande à haute élévation et transstockeurs manuels. Tous sont présentés dans la section « Engins de manutention ». Avec ces systèmes, il est primordial d’atteindre un haut niveau de rationalisation pour obtenir une capacité de stockage maximale. L’utilisation de convoyeurs à rouleaux, de transpalettes, de chariots, voire de véhicules à guidage automatique et laserguidés (AGV et LGV) est indispensable pour atteindre cet objectif.
Un autre aspect fondamental à prendre en compte est l’ergonomie des postes de travail, notamment lors des opérations de picking et de chargement de la marchandise dans les rayonnages. L’opérateur doit pouvoir se déplacer verticalement et horizontalement entre les rayonnages, en toute sécurité et de manière optimale.
En outre, l’opérateur possède d’autres dispositifs pour atteindre des taux de productivité élevé. Parmi ceux-ci, l’intégration d’un logiciel de gestion d’entrepôt (WMS) performant et l’utilisation de terminaux de radiofréquence facilitent la réalisation des opérations et ce, sans commettre d’erreurs, et permettent également de traiter simultanément plusieurs commandes.
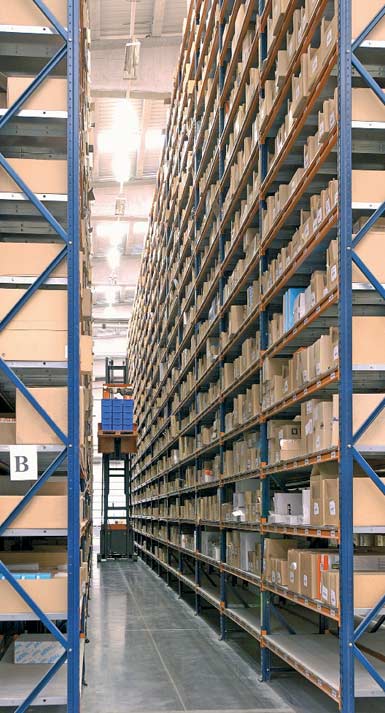
Rayonnages à allées étroites
- Evaluation de ce système :
Paramètres | Evaluation | Remarques |
Coût total de l'investissement | 3 | Moyen. L’investissement peut sembler assez élevé mais est supportable grâce à l’amélioration et l’optimisation d’autres paramètres |
Coût de la manutention | 2 | Faible. Toutes les opérations sont réalisées avec des engins de manutention motorisés, le coût de la main d’œuvre est ainsi réduit |
Capacité de traitement | 5 | Moyenne. Ce paramètre croît de façon spectaculaire compte tenu de la rapidité des opérations obtenue avec ce système |
Exploitation de la surface | 6 | Elevé, le taux d’occupation est élevé grâce à la faible largeur des allées et à l’exploitation de toute la hauteur disponible de l’entrepôt |
-
Les rayonnages dynamiques pour picking
Avec le principe du « produit vers l’homme », la solution de stockage pour les articles de petites dimensions avec laquelle on obtient les meilleures performances est celle des rayonnages dynamiques pour picking.
Chacun des bacs donnant sur l’allée de préparation des commandes contient une seule référence, les bacs de réserves étant placés derrière. Le nombre d’allées nécessaires est considérablement réduit, tout comme la distance à parcourir par chaque opérateur.
Grâce à la réduction de l’espace minimal requis pour les allées, la surface exploitée au sol est bien plus grande que n’importe quel autre type de système.
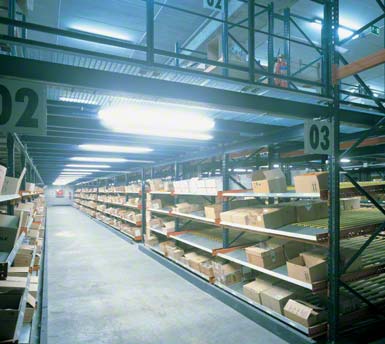
(A) Rayonnages dynamiques pour picking d'une entreprise de retail aéroportuaire
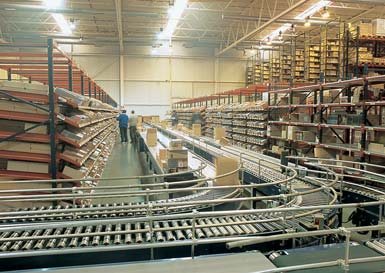
(B) Rayonnages dynamiques pour picking et convoyeurs à rouleaux d'une socité de reproduction discographique
La préparation de commandes peut être opérée de trois façon différentes :
- La plus simple est d’utiliser un chariot (ou un préparateur de commandes) avec lequel l’opérateur se déplace dans les rayonnages pour préparer la commande.
- La seconde possibilité consiste à installer un circuit de convoyeurs sur l’un des côtés de l’allée, aligné au rayonnage.
- Enfin, la troisième option est également d’installer un circuit de convoyeurs, mais au milieu de l’allée. Dans ce cas, la priorité est donnée à la productivité plutôt qu’à la capacité de stockage (comme montré sur la photo B).
Les diverses possibilités de configuration permettent d’adapter les rayonnages dynamiques pour picking à des besoins différents. Par exemple, les niveaux supérieurs peuvent être aménagés pour le stockage de palettes contenant la marchandise de réserve, ou combiner le picking sur des rayonnages dynamiques pour palettes et pour bacs.
Il est possible d’améliorer les solutions de stockage pour picking grâce à l’installation de dispositifs pick-to-light gérés et contrôlés par un logiciel de gestion d’entrepôt. En indiquant l’emplacement et la quantité de marchandises à extraire, le nombre de commandes préparé par cycle est supérieur.
Les systèmes de stockage pour picking sur rayonnages dynamiques sont indispensables pour gérer un volume important de commandes avec de nombreuses références. S’ils sont associés à des dispositifs pick-to-light , alors ils se rapprochent fortement de la préparation de commande automatique, basée sur le principe du « produit vers l’homme ». En réalité, les rayonnages pour picking avec dispositifs pick-to-light sont fréquemment installés aux abords d’un magasin automatique ou de carrousels horizontaux, surtout pour la préparation de commandes de produits de grande consommation. Dans ce cas, le picking dynamique est considéré comme faisant partie intégrante des éléments automatisés de l’entrepôt.
- Evaluation du système :
Paramètres | Evaluation | Remarques |
Coût total de l'investissement | 8 | Moyen. L’investissement est moyen, bien qu’il soit évalué à 8, mais son coût est compensé par les avantages et l’efficacité de ce système. |
Coût de la manutention | 2 | Faible. Ce système améliore l’efficacité et les performances des opérateurs. |
Capacité de traitement | 8 | Elevé. La capacité de traitement est très élevée dans les environnements où les opérations sont nombreuses, en particulier avec l’utilisation de dispositifs pick-to-light. |
Exploitation de la surface | 8 | Elevé, le taux est très élevé en raison du nombre réduit d’allées. L’exploitation de la hauteur de l’entrepôt n’est pas nécessaire mis à part pour le stockage de palettes de réserve, au-dessus des rayonnages pour picking. |
2. Le principe du produit vers l'homme
Ce principe, radicalement opposé au principe de « l’homme vers le produit », consiste à rapprocher au maximum les unités de l’opérateur afin qu’il se déplace le moins possible. Cette méthode permet de supprimer les temps morts existants lors d’un déplacement entre une opération de réapprovisionnement et une autre de picking.
Contrairement aux systèmes présentés précédemment, bien que le réapprovisionnement et la préparation de commandes soit réalisés manuellement, le déplacement des unités de charge est quant à lui presque entièrement automatisé.
Les systèmes de stockage compatibles avec le principe du « produit vers l’homme » sont les transstockeurs pour bacs (Miniload), le stockage vertical et les carrousels horizontaux.
-
Les transstockeurs pour bacs (miniload)
Le système Miniload est un magasin automatique pour bacs composé essentiellement de rayonnages par accumulation, alimenté en marchandises par un transstockeur. Les unités manipulées par ce système sont des bacs ou des cartons d’une dimension de 600 x 400 m ou 800 x 600 mm, adaptés au stockage de petites pièces.
Ce système est également compatible pour la manipulation de plateaux à la place des bacs pour stocker des produits de très petite taille, formant ainsi une mini unité de charge. C’est d’ailleurs à cela qu’il doit son nom : miniload.
Ce système de stockage exige peu de surface et, comme il répond au principe du produit vers l’homme, il permet la configuration de postes de travail ergonomiques et performants. Les Miniloads peuvent également être combinés de sorte qu’un seul opérateur est nécessaire pour contrôler tous les appareils.
La charge maximale supportée par ce système est de 100 kg par unité (bac, conteneur ou plateau) et peut atteindre des vitesses de levage (jusqu’à 90m/min) et déplacement horizontal (jusqu’à 250m/min) élevés.
Dans ce type de système, l’un des principaux avantages est le contrôle du stock. Généralement, les articles sont identifiés grâce à des codes-barres lus par des scanners. Le système informatique du Miniload assure, quant à lui, le contrôle et la gestion des marchandises, ainsi que les opérations à réaliser.
Il existe, pour les miniloads, différentes configurations possibles avec des capacités et des vitesses variables. Ces configurations permettent d’adapter la solution aux besoins de chaque entreprise ou industrie.
Les miniloads sont classés selon 3 types de rendement : moyen, élevé et très élevé.
- Les miniloads à rendement moyen sont capables de déplacer un maximum de 150 bacs par heure (75 entrées et 75 sorties) en cycle combiné (mouvement permettant d’introduire une unité de charge pour ensuite en extraire une autre, ou inversement). Comme dans le cas des transstockeurs pour palettes, un côté des rayonnages, dans une allée parallèle, peut comprendre des niveaux dynamiques inclinés pour le picking de références à rotation A, tandis que les références à rotation B et C sont situés en tête du magasin Miniload. Il est également possible d’installer des dispositifs put-to-light et pick-to-light afin d’accélérer les opérations.
- Les miniloads à rendement élevé peuvent déplacer entre 150 et 180 bacs par heure, en cycle combiné. De même que le type précédent, il est possible d’avoir recours à des rayonnages dynamiques sur l’un des côtés. Ce type de Miniload permet également d’avoir plusieurs postes de picking en périphérie du magasin, si cela est nécessaire, et exige l’installation de dispositifs pick-to-light et put-to-light .
- Enfin, les miniloads à rendement très élevé déplacent jusqu’à 250 bacs entrants et 250 bacs sortants par heure, en cycle combiné. Avec ce modèle, seuls les bacs en tête de magasin sont approvisionnés en marchandises et les postes de picking peuvent être aménagés dans une zone annexe. Dans ce type d’installation, il est essentiel de mettre en place des mesures ergonomiques, des systèmes d’aides intuitifs ainsi qu’un logiciel de gestion d’entrepôt avancé. En raison de leurs caractéristiques, les Miniloads à rendement très élevé sont une solution optimale pour la gestion de nombreux bacs sur des périodes très courtes. C’est pourquoi, leur utilisation est idéale pour les entrepôts tampon de commandes préparées, les entrepôts qui approvisionnent les postes de montage ou de manutention, et comme séquenceur pour livrer rapidement les bacs commandés.
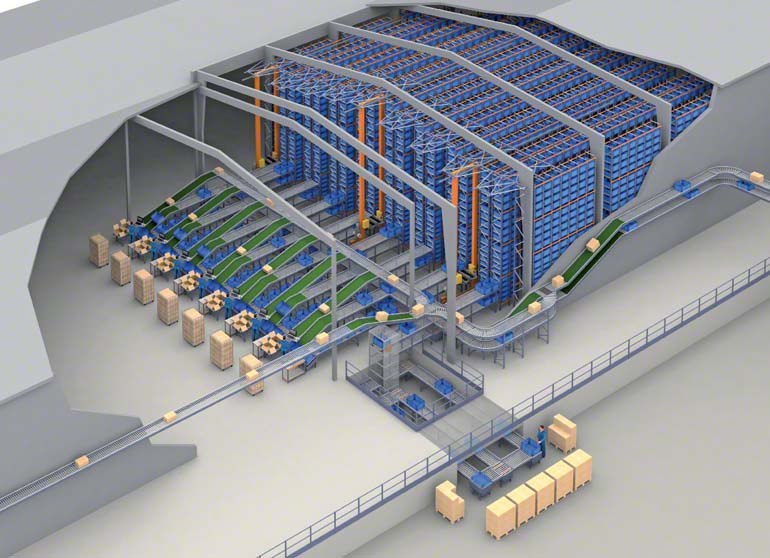
Magasin automatique pour bacs, miniload, à rendement très élevé
- Evaluation de ce système :
Paramètres | Evaluation | Remarques |
Coût total de l'investissement | 7 | Moyen, avec une tendance à la hausse |
Coût de la manutention | 1 | Faible. Comme il s’agit d’un système presqu’entièrement automatisé, l’impact du coût de la main d’œuvre sur celui de la manutention est quasi nul |
Capacité de traitement | 6 | Moyen. L’indice de capacité de traitement est moyen, avec une tendance à la hausse plus ou moins importante selon le modèle choisi |
Exploitation de la surface | 8 | Elevé. La capacité de stockage est très élevée par rapport à la surface au sol nécessaire. Il peut, en effet, occuper toute la hauteur de l’entrepôt |
-
Les systèmes de stockage verticaux et carrousels horizontaux
Bien qu’actuellement, le système le plus utilisé soit le miniload, les systèmes de stockage verticaux et les carrousels horizontaux existent toujours.
-
Le principal avantage des systèmes de stockage verticaux est l’utilisation plus importante de l’espace vertical disponible, c’est-à-dire, en hauteur. Ils sont particulièrement adaptés lorsque la surface disponible est limitée mais où il est possible d’optimiser la hauteur du bâtiment. Ce sont des structures fermées, basées sur le principe du produit vers l’homme, évitant aux opérateurs de se déplacer pour manipuler les charges.
-
Les carrousels (tant horizontaux que verticaux) reposent sur un système mécanique interne pour transporter les marchandises jusqu’à l’opérateur, en charge de les extraire sans avoir à se déplacer.
Ces systèmes de stockage sont de moins en moins utilisés, mais ils restent intéressants de les connaître car ils sont toujours employés dans certains entrepôts.