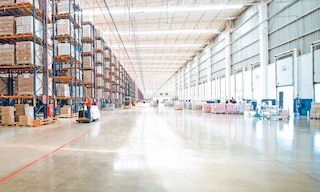
Dock to Stock : l'efficacité commence sur le quai de l'entrepôt
Combien de temps dois-je stocker la marchandise que je viens de recevoir à l'entrepôt ? Ce processus, connu sous le nom de dock to stock (en français, du quai de chargement à l'entrepôt), fait référence à toutes les opérations intervenant entre la réception et le stockage de la marchandise. L'optimiser est la première étape à franchir pour disposer de processus logistiques efficaces.
Dans cet article, nous analyserons son importance et les étapes qui le composent. De même, nous expliquerons comment automatiser au maximum ce processus, en réduisant ainsi la durée du cycle.
Qu'est-ce que le « Dock to Stock » ?
Le dock to stock fait référence au processus qui démarre lorsque l'entrepôt reçoit la marchandise sur les quais et qui s'achève une fois que celle-ci est stockée dans les rayonnages. Cette opération est jalonnée par différentes étapes déterminant l'efficacité du fonctionnement de l'entrepôt.
Parmi celles-ci, la plus complexe est la gestion du stock, comprenant la validation et l'inclusion de la nouvelle marchandise dans l'inventaire. De fait, la plupart des entrepôts utilisent actuellement un WMS afin d'accélérer ce processus.
Mais, combien de temps doit mettre un entrepôt à déposer la marchandise sur les rayonnages après l'avoir reçue ? Selon les données de l'organisation américaine American Productivity & Quality Center (APQC), les entrepôts les plus efficaces consacrent moins de quatre heures au processus de dock to stock, tandis que d'autres centres logistiques ont besoin de 48 heures au maximum.
Le procédé de « Dock to Stock »
Voici les opérations internes participant directement à ce procédé à partir du moment où l’entrepôt reçoit la marchandise sur les quais de chargement jusqu'à ce qu'elle soit stockée dans les rayonnages :
- La réception : les camions contenant de la marchandise en provenance des sites de production ou des fournisseurs arrivent aux quais de chargement. Les palettes sont déchargées du camion et sont provisoirement posées au sol.
- La validation de la marchandise : les opérateurs vérifient que le fournisseur ou l'usine a envoyé les bonnes quantités d'articles et que ceux-ci sont en bon état. Ils vérifient ensuite que la marchandise est en conformité avec les spécifications physiques établies.
- La mise à jour du stock : tout le matériel reçu doit être enregistré dans l'inventaire de l'entrepôt.
- Le stockage : la marchandise est déposée dans l'unité de charge (palette, bac ou conteneur), puis dans le système de stockage correspondant en prenant en compte les critères de rotation du stock.
Tout incident ou retard dans l'une de ces opérations a des répercussions négatives sur la durée du cycle du dock to stock.
Comment raccourcir la durée du cycle du « Dock to Stock » ?
Réduire la durée du cycle nécessaire à l’achèvement du processus de dock to stock est fondamental pour obtenir une chaîne logistique efficace. Un certain nombre d'éléments interviennent au cours de ce processus. Les optimiser permettra d'améliorer la productivité du dock to stock. Pour ce faire, il faut prendre en compte les éléments suivants :
- La conception de l'entrepôt : la zone des quais de chargement doit être aménagée de sorte à recevoir les camions rapidement et en continu afin que ceux-ci n'aient pas à attendre pour effectuer le déchargement. Il est aussi important de définir, dans l’entrepôt, la surface destinée au stockage des palettes au sol.
- La diminution des déplacements des employés : la distance parcourue par les opérateurs durant l'exécution des opérations est directement proportionnelle à la durée du cycle du dock to stock. Le fait de définir l'ordre des tâches de réception et de les centraliser aide à optimiser l'itinéraire interne des opérateurs.
- L'accélération de la gestion de l’information : il s'agit, sans aucun doute, de l'opération la plus fastidieuse et importante de toutes. Les erreurs à ce stade affectent la gestion intégrale du stock. Mettre en œuvre un WMS constitue la meilleure solution pour accélérer ce processus.
- L'automatisation : disposer d'engins de manutention et de systèmes de stockage automatisés raccourcit la durée du cycle du dock to stock. En réalité, il est possible d'automatiser toutes les opérations participant à ce processus.
- Le cross-docking : une bonne gestion du stock permet de savoir si l'on doit ou pas stocker un produit que l'on vient de recevoir. Le cross-docking évitera de perdre du temps dans l'exécution de tâches de stockage qui ne sont pas indispensables.
D'une façon générale, si l'on souhaite raccourcir la durée du cycle du dock to stock, il est primordial de mettre en œuvre une logistique efficiente, en faisant attention à tous les éléments participant à ce procédé.
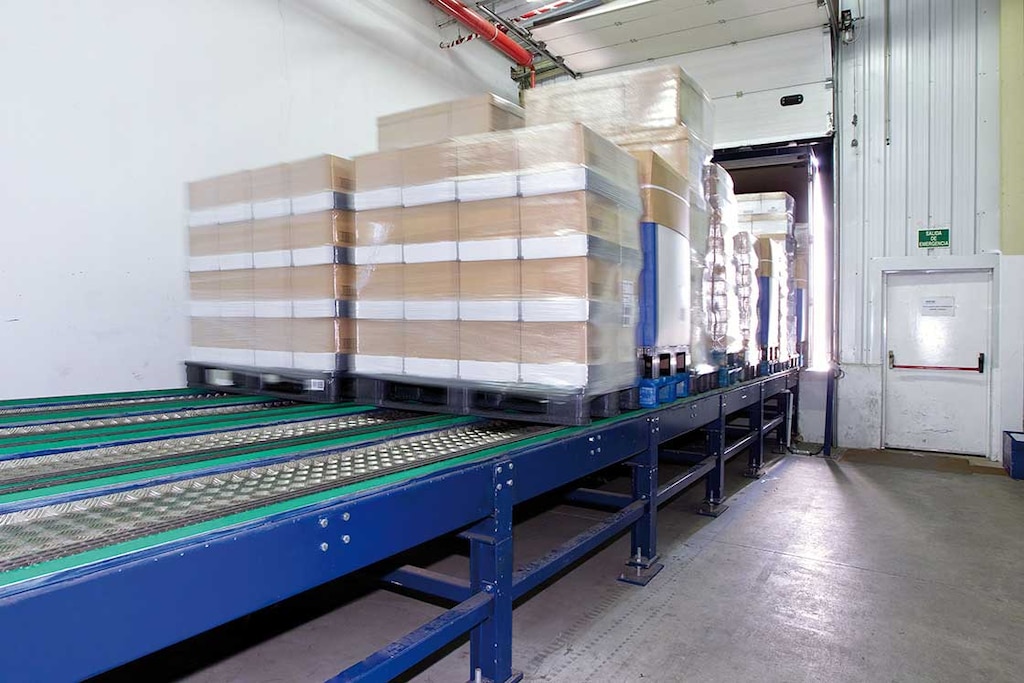
Le processus « Dock to Stock » automatisé
Les engins de manutention et les systèmes de stockage automatisés contribuent à réduire au maximum la durée du cycle employé dans le dock to stock. Il est actuellement possible d'automatiser ce processus du début jusqu'à la fin.
Chaque entreprise doit évaluer, en fonction de ses besoins, s'il est plus rentable de robotiser tout le processus ou seulement une des opérations, au moyen d'éléments comme des plateformes de déchargement automatique, des convoyeurs, des postes d'inspection d'entrée ou encore des transstockeurs.
L'automatisation permet à l'entrepôt de fonctionner 24/7, sans interruptions. La diminution des erreurs et, par conséquent, des coûts, est un autre des principaux avantages de ce procédé. La robotisation réduit de manière drastique les erreurs découlant de la gestion manuelle, en garantissant l'efficacité maximale dans toutes les opérations auxquelles elle est intégrée. En somme, l'automatisation du dock to stock est une des solutions les plus efficaces pour augmenter la productivité, améliorer la qualité du service et réduire au maximum les coûts d'exploitation de l'entrepôt.
Un logiciel pour le « Dock to Stock »
Les WMS, comme Easy WMS, contribuent à l'augmentation de la productivité de toutes ces opérations. En plus de lire et de vérifier les articles, de les introduire dans le stock et de leur assigner un emplacement en fonction des stratégies de rotation, le WMS peut savoir à l'avance les articles qui vont être reçus (ASN, Advanced Shipping Notifications).
De la sorte, et étant donné que les données figurent déjà dans le système, il est possible d'élaborer les stratégies de réception de la marchandise en fonction de s'il s'agit de conteneurs complets, de marchandise multiréférencée, voire de réceptions aveugles.
Easy WMS propose différents modules permettant d’adapter le logiciel aux exigences logistiques et donc d'améliorer considérablement le procédé dock to stock. C'est le cas de Supply Chain Analytics, qui segmente et trie une grande quantité de données chaque jour pour les transformer en informations utiles. Ce logiciel crée des KPI personnalisés comme : le nombre de réceptions par heure, le pourcentage de marchandise abîmée, le taux d'occupation de l'entrepôt, etc.
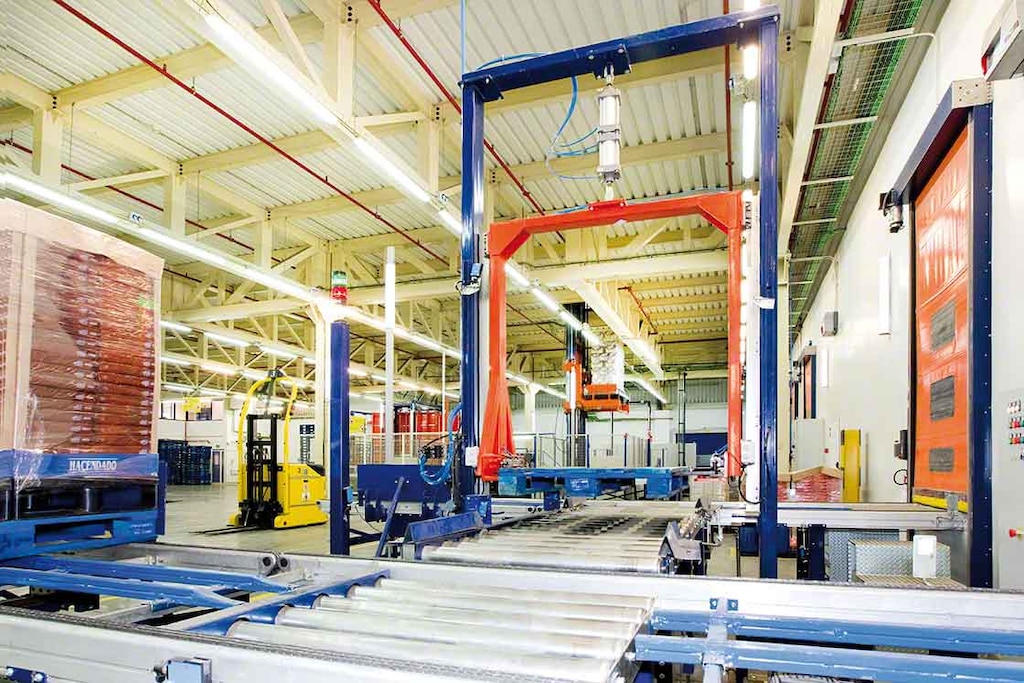
La première étape pour obtenir un entrepôt efficient
Le dock to stock est le premier défi logistique qu'un entrepôt doit relever avant d'effectuer les autres opérations. Il est impossible de préparer les commandes et de les expédier pour qu'elles arrivent au client dans les temps s'il y a, au préalable, des problèmes au niveau de la réception, de la gestion du stock et du stockage.
Il est impossible de construire une maison en commençant par le toit, tout comme il est impossible d'effectuer correctement une livraison de commandes sans des processus de réception et de stockage efficaces. Ainsi donc, en cas de difficulté dans la communication avec les fournisseurs, la gestion du stock ou les critères de rotation pour stocker la marchandise, n'hésitez pas à contacter Mecalux pour que nous vous conseillions et vous aidions à optimiser vos processus logistiques.